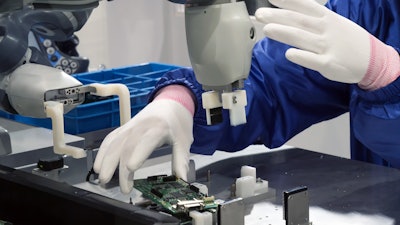
In many cases, manufacturers that have embraced robotics have experienced exceptional results. However, unless design engineers understand the full scope of a facility’s processes and people, their cobot design may fall short of expectations in terms of maximum efficiency gains. Will this trend continue as the levels of automation in this industry rise?
How Better Design Leads to Greater Efficiency
Decades ago, simply integrating robotics into production and assembly lines was enough to realize efficiency and revenue gains. Now that it has become a sector staple — an estimated 90% of all robots in operation today are located in manufacturing facilities — outperforming the competition requires strategy.
Many leaders have taken to optimizing during the research and development stage to secure a competitive edge. Collaborative robots (cobots) have emerged because of this advancement. They have shown to be among the most effective robotics subsets thanks to their novel ability to work alongside human technicians.
Cobot design enables unparalleled levels of automation in the manufacturing industry. Unlike industrial robots, these machines can be reprogrammed at will and placed almost anywhere. They can often perform faster than their human counterparts. Manufacturers can repurpose or move them as necessary to accommodate factory floor alterations or labor availability changes.
Numerous real-world case studies prove these machines can increase a facility’s productivity level. In the case of one spot welding cobot, technicians were able to produce 100 tool trays in 2.5 hours instead of their typical eight after implementation.
Ideally, every manufacturer would realize such efficiency gains post-implementation. However, poor design — whether through misguided model selection or ill-informed research and development — often leaves them coming up short. Even if a machine inherently outperforms its human counterparts, it still won’t reach its full potential without strategic integration.
Successfully Integrate your Cobot
Many business leaders don’t consider cobot design as critically as they should. Instead, they focus on this technology through the broader context of automation. They often decide to adopt it after witnessing it in action or hearing about it via market reports, assuming it will automatically increase their productivity and throughput as it has done for others.
These people are technically correct since almost any modern robot can outpace human workers. According to the United States Bureau of Labor Statistics, the manufacturing sector’s labor productivity increased at an annualized rate of 0.3% from 2019 to 2024 — far below the long-term rate of 2.1% from 1987 to 2024.
However, manufacturers set themselves up for failure when they give little thought to the reason or strategy behind implementation. A cobot’s hardware, compatibility, looks and placement cumulatively affect its repeatability, ease of programming, usability and performance, which, in turn, impact its efficiency.
Even if business leaders carefully contemplate model and feature selection during integration, they should revisit their cobot’s design every few years. As expectations for robotics and levels of automation in the industry evolve, existing machines should be repurposed or reprogrammed. The point isn’t just about evading legacy technology — they must consider the human factor.
Aligning technology with the workforce’s expectations is critical in determining the success of a human-reliant machine. Cobots’ uniqueness necessitates periodic design changes. Unlike conventional industrial robots, they must adapt alongside their human operators to drive interest, ensure safety and facilitate strong relationships.
Consider Manufacturing Workers’ Roles
Design engineers can generally overlook the human factor when designing industrial robots without significant consequences. They can disregard considerations like whether the exterior is visually appealing or whether people will connect with it. Crucially, they don’t have that luxury when creating cobot schematics.
Rising levels of automation in the manufacturing industry have the workforce on edge. Even though many companies are experiencing a persistent skill shortage, many workers fear being replaced by machines. If design engineers were to overlook the human factor when building cobots, they’d likely dissolve trust and cultivate hesitancy, impacting implementation effectiveness.
This reality isn’t hypothetical. Approximately 50%-75% of automation implementation attempts fail in terms of reliability, flexibility or quality, mainly due to disregard for human-centric factors. Statistically, employee buy-in could be the difference between a facility struggling to achieve a return on investment or achieving unparalleled efficiency rates.
Factors to Consider for a Better Cobot Design
Design engineers should consider how their components influence workers' perceptions and interactions with their cobot design. For starters, tactile, vision, force-torque and proximity sensors should be present and have some visual or auditory indicator accompanying actions. If humans can understand the machine’s intentions, they’ll feel safer working alongside it.
For this reason, control algorithms and feedback loops are just as important. Data-driven decision-making enhances accuracy, enabling cobots to act with precision. Designing them to be able to adjust their movement, trajectory, speed and force continuously helps cultivate confidence within staff, driving seamless interactions that increase efficiency.
As most design engineers are aware, cobots are not inherently safe, despite what their name suggests. Safety is application-dependent — giving a robot too much freedom is dangerous. Slowing it down or limiting its flexibility may seem counterproductive, but fostering confidence generates long-term efficiency gains more consistently than letting it intimidate workers.
One commonly overlooked design factor is the crews themselves. Professionals must recognize they routinely do work beyond the scope of their contract, whether that involves reorienting a part on the assembly line or double-checking for defects. Unless they account for metrics like these, manufacturers will have unexplained performance indicator changes.
Design engineers should discuss day-to-day operations with assembly and production line staff to ensure their design is accurate. Their machine can only operate at the precise baseline for the role it’s supplementing if they have comprehensive visibility. This way, it can more readily surpass typical performance and production rates.
Enhance Your Production with Strategic Cobot Design
Since design engineering professionals consider countless data points when developing their schematics, they tend to overlook human-centric factors. If cobots are to become a staple in the manufacturing sector, they must reconsider how they approach their typical processes. The workforce will only embrace robotics if they trust these machines.