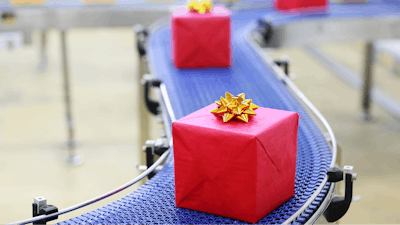
When manufacturers turn to intelligent automation resources, such as robotic process automation and LoCode platforms, their main goal is typically to lower costs by automating manual tasks, enabling them to reallocate resources and reassign employees to more meaningful work. On the surface, this sounds like it should be easy enough to track. Many companies simply calculate return on their automation investment by estimating the cost for building out a new automation, the cost to maintain that automation, and then the estimated time savings provided by automating what was once a manual task.
While this may appear to be a fairly straightforward approach, there are several factors which can complicate this seemingly simple formula. Here are six factors manufacturers should always consider when trying to determine ROI on intelligent automation projects.
- Redundant Automations. On average, 20-30 percent of an established automation estate is redundant or wasteful. When manufacturers calculate the success of their automation practice, they often look at it on an individual bot level by considering how much that one bot is saving the company. Due to an overall lack of governance, though, many manufacturers face redundant automations, poor quality automations, and other issues that cost them money on a holistic level – much of which they may not even realize.
- Maintenance Costs. Many manufacturers underestimate maintenance costs, which can result in a very inaccurate picture of the success of any automation. High break-fix costs, for example, can result in once-successful automations shifting from the benefit column to a liability. This typically happens when complex automations run into errors or stop working altogether. Getting them back on track requires a high skill level, which can be difficult to impossible to calculate at the beginning of a new automation project. Similarly, the cost to change out an application across a company’s entire portfolio can be extremely expensive. Switching from Outlook to Google Mail, for example, may seem easy enough on paper, but can quickly turn into an expensive project which, in the process, significantly lowers the ROI of the entire automation practice.
- Application Licensing Costs. When manufacturers consider licensing costs for an RPA bot, they often think only in terms of the licensing fee for the actual RPA platform. What they forget in this calculation is the fact that an automation is essentially a digital worker and, like any human worker, it requires access to a wide array of technology systems, such as Microsoft Outlook, the company’s ERP system, billing tools, and more – all of which come at a price. That licensing cost for any software systems that the bot will need to access represents a major cost driver for an automation and must be factored into the overall ROI calculations. Just to provide an example of how expensive this can be, one bot for a complex automation can easily cost more than $200 per month in licensing fees. That adds up to a huge annual cost, which some manufacturers fail to account for in calculating ROI for an intelligent automation project.
- Inflated RPA Platforming Fees. As RPA technologies continue to evolve, their costs tend to rise. For example, RPA platforms which have acquired new technology, such as process mining tools, typically lead to higher operational expenditures. Similarly, an RPA technology like Automation Anywhere, which forced users to shift to a Cloud version of their product, led to a significant increase in resource costs. Since such technology evolutions are inevitable, manufacturers should regularly recalculate their intelligent automation ROI to take into account any changes in core RPA fees.
- Inflating RPA Resource Costs. As a manufacturer’s RPA practice grows, so too will its resource costs, just like any other business function. Moreover, as new automations are created, additional senior RPA resources may need to be hired – all of which increase the overall cost it takes to deliver and maintain an RPA bot. Unfortunately, many manufacturers fail to account for these rising resource costs and mistakenly continue to rely on their older estimated costs to determine ROI.
- RPA Design and Compliance Time Designing a new intelligent automation typically requires numerous resources, including experts who know and understand the process inside and out, IT personnel, and other important stakeholders across the organization. The costs for all of these people and the time it takes for the initial meetings required to develop the bot can add up quickly. Sadly, it is a cost that manufacturers often neglect to factor into their overall ROI calculations. It is essential for companies to recognize that the cost of building a bot must also account for the cost to learn about the process, design the bot, understand any security risks, review it with all stakeholders, and assess it for any compliance risks.
These and other factors – including a reduction in manual errors and increases in productivity – need to be considered by manufacturers when calculating ROI for an intelligent automation project. If they are not accurately assessed at the beginning of a project, they will always find a way to eventually surface, bringing with them added costs which ultimately undermine the ROI that was originally calculated.
Irina Lunin is the Vice President of Research & Development at Blueprint Software Systems.. For more information, visit https://www.blueprintsys.com.