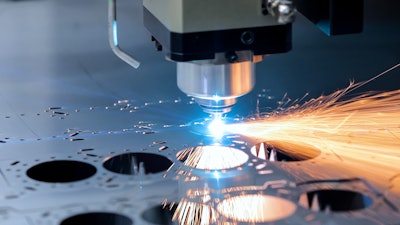
Few innovations have impacted machining shops as much as CNC equipment. These automation solutions have significantly improved production times and product quality, so it’s no surprise they’ve become the industry standard. Artificial intelligence (AI) in CNC machining could take those benefits even further.
Organizations in virtually every industry have rushed to implement AI, achieving varying degrees of success. While it’s important to recognize that AI is not an easy fix for all problems, CNC machining is uniquely situated to gain much from it.
Applications of AI in CNC Machining
Capitalizing on the potential of AI in CNC programming starts with recognizing where it can improve machining workflows. Conveniently, AI use cases apply to multiple stages throughout the CNC process.
Improved CAD Models
At the top of the workflow, you can use AI assistance to optimize CAD models before sending them to a CNC mill. Many CAD software providers offer generative design, which uses AI to suggest possible designs or propose changes to existing ones to better meet a project’s goals.
In some instances, generative design has compared as many as 10,000 iterations in just a few days. As a result, teams can find the ideal layout for their projects with high confidence without rigorous and expensive manual, real-world testing. These results came from an architecture firm, so CNC machining — which occurs on a much smaller scale — could see even shorter timelines.
AI is helpful in this area because it outperforms humans when finding subtle trends and connections in vast datasets. Consequently, it can spot opportunities to improve designs humans may miss. It also compares data faster and more accurately than humans, lowering costs and preventing rework.
Optimized CAM Performance
Computer-aided manufacturing (CAM) can see similar results from AI CNC programming. CNC machines’ automated nature means they already reduce human error and prevent waste, but they still leave room for mistakes. The programming process is still manual, but you can automate it through AI to further improve accuracy and efficiency.
Just as AI can analyze project targets to suggest an ideal design, it can determine optimal CNC parameters by analyzing a CAD model. That includes simulating various options to find which combination of controls would produce the product most accurately in the least amount of time.
Because AI works off real-world data, it’s more likely to make accurate decisions about which parameters suit a given cut the best. It’s also less inclined to make mistakes in repetitive, data-heavy workflows like writing G-code. Human experts may need to sign off on the code before running the machine, but the process is still faster.
Predictive Maintenance
AI in CNC machining has benefits outside of the actual cutting process. One of the most advantageous of these secondary use cases is predictive maintenance (PdM). Here, machine learning models analyze CNC machines’ performance to detect issues before they’re noticeable to workers.
Maintenance can cost up to 70% of the price of goods sold in this industry. Consequently, there’s a lot to gain from catching disrepair earlier. Because AI can detect minor abnormalities in data, it does a much better job of preventing breakdowns than humans.
While all preventive maintenance can minimize repair costs, conventional approaches result in unnecessary downtime spent inspecting machines in perfect health. By contrast, PdM lets you only take a CNC mill offline when you know it needs fixing. As a result, you can ensure all maintenance-related downtime and spending produces real value.
Automated Quality Control
Another secondary application of AI in CNC machining is to automate post-cutting quality inspections. While such checks are essential, they usually create bottlenecks in production. AI can minimize those inefficiencies by analyzing a product faster than humanly possible.
Some facilities have reduced inspection times from six hours to just two after implementing an AI-powered automated solution. AI works so quickly because it can measure multiple factors simultaneously. Comparing the measurements to data on acceptable parameters can likewise happen in near-real time.
In addition to being faster, AI is also more reliable than manual quality control. These systems judge each product against the same information every time, so they maintain an even level of accuracy with every inspection. Using data instead of intuition or experience makes them more objective, resulting in fewer missed flaws.
Making the Most of AI in CNC Programming
Given all this potential, applying AI across the entire CNC workflow at once can be tempting. However, over 80% of AI projects fail, mostly due to implementation issues. Consequently, you must recognize a few common obstacles and adopt a more careful approach to ensure a positive return on investment.
Three of the five most common causes of AI failures boil down to not applying AI where it can address real-world, relevant problems your business faces. Don’t embrace the technology just to have it or integrate it where you see competitors using it. Rather, identify your largest inefficiencies and compare them to AI’s capabilities to find where it’s most valuable.
Optimal AI applications tend to be in highly repetitive or detail-oriented tasks. It’s also best when used in places where you can supply a lot of relevant data for it to make informed analyses. CAD optimization and CNC programming tend to fall into these categories because you can find ready-made, pretrained AI models in this software. However, if your shop loses money to maintenance or rework, PdM or quality control automation may deserve your attention first.
You can likely benefit from multiple AI applications in CNC machining. However, start with your biggest opportunity to improve and only invest in new use cases once the initial project shows a positive ROI. A gradual strategy will balance tech costs and help you learn the ropes of AI before spending too much on it.
Finally, remember that AI is a complement to your human workforce, not a replacement. A worrying 37% of companies using AI have already replaced employees with it, but this technology and human professionals possess separate skill sets. You’ll build a better workforce and get more from AI if you use it as a tool to increase worker productivity, not as a direct stand-in.
AI CNC Machining Will Change the Industry
AI CNC machining will become mainstream before too long, rewriting the industry like CNC milling once did. The advantages are too substantial to overlook.
You must learn how to capitalize on AI’s potential early to stay ahead of the competition. That begins with recognizing where you can use this technology and how it can benefit you.