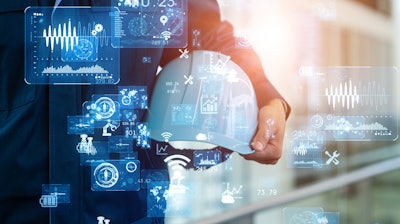
OSHA has found that American companies lose billions of dollars each year as a result of injuries, illnesses, and fatalities, noting that employers who implement effective safety and health programs may expect to minimize the costs associated with these injuries and illnesses. Economic cost aside, there is also an intangible cost in terms of the immeasurable human suffering caused by occupational accidents and work-related diseases.
OSHA has grouped all workplace hazards into the following six categories:
- Safety hazards..
- Work organization hazards.
- Biological hazards.
- Chemical and dust hazards.
- Ergonomic hazards.
- Physical hazards.
Of all these hazards, OSHA opines that safety hazards are the most common and will be present in most workplaces at one time or another. Safety hazards include:
- Spills on floors or tripping hazards, including blocked aisles or cords running across the floor.
- Working from heights such as scaffolds, ladders, roofs, or any elevated work area.
- Unguarded machinery and moving machinery components; guards removed or moving components that workers can accidentally touch.
- Electrical hazards such as improper wiring, frayed cords, and missing ground pins.
- Confined spaces.
- Machinery-related hazards (forklifts, lockout/tagout, and boiler safety, among others).
Dealing with the Unexpected
According to OSHA, an emergency action plan (EAP) is recommended for all employers because it can help facilitate and organize employer and employee actions in times of workplace emergencies. Employees need to understand the differences between CPR and AED, and which health emergency requires which immediate response.
Well-developed emergency plans and adequate employee training (so that they understand their roles and responsibilities in the plan) will bring about fewer and less severe injuries, as well as less damage to the workplace during emergencies. A poorly articulated plan may result in a disorganized evacuation or emergency response which can lead to confusion, injury, illness, and/or property damage.
Preparing a comprehensive emergency action plan involves carrying out a hazard assessment to determine if there are any hazards inside or outside the workplace that could cause an emergency. The plan should clearly explain how employees will respond to different types of emergencies, taking cognizance of the organization’s specific worksite layouts, structural features, and emergency systems. If the organization has more than one worksite, each of them should have its own EAP.
Though not all employers are required to have an EAP, developing one is a good way to protect employees and businesses during emergency situations. Effective controls enable employers to provide their employees with safe and healthful working conditions, thus protecting them. To control and prevent hazards effectively, OSHA recommends:
- Involving employees who often have the best understanding of the conditions that bring about hazards, as well as insights into how such hazards can be controlled.
- Identify and evaluate options for hazard control, using a "hierarchy of controls."
- Work with a hazard control plan aimed at guiding the selection and implementation of controls, and implement those controls based on the plan.
- Develop plans with measures aimed at protecting employees in times of emergencies and non-routine activities.
- Evaluate the effectiveness of existing controls to determine whether they continue to offer protection or whether different controls may yield better results.
- Review new technologies for their potential to offer better protection, be more reliable, or be less expensive.
The Future of Industrial Safety
It is the view of many that the world of work is presently undergoing a fourth industrial revolution, driven by the digitalization of information and advanced connectivity.
One key impact of these new realities on safety is that technological developments have, in some cases, taken over dangerous jobs previously done by human workers. A related development is the growth in the adoption of AI to increasingly support employee safety and health in other ways, such as in medical diagnosis. However, the replacement of human workers by technological creations can have implications for job security and employee well-being. This is because job insecurity, unemployment, or underemployment can impact a worker’s psycho-social health.
Also, with the increasing popularity of hybrid and remote work, it is likely that in the future workers will increasingly work outside of traditional workplaces. While this may nullify the threat from hazardous workplaces, it may also introduce new risks emerging from the growing trend of human-machine collaboration, including ergonomic risks (such as those that may arise from the increased use of mobile devices and sedentary work) and cognitive load.
Wearable smart devices and other smart technologies are also sources of opportunities when it comes to safety and health. Such devices and technologies enable safety managers to monitor workplace behavior and to communicate safety and health advice and information in real-time. These devices are also capable of monitoring employee fatigue, fall detection and air quality. Wearable and IoT-based fatigue monitoring can detect “microsleeps” in truck drivers and operators of heavy machinery.
Amazon holds a patent for a wristband that tracks the location of warehouse workers and vibrates to ‘nudge’ them toward the direction of their next task.
OSHA has used drones for unmanned aerial inspections, often when it is not safe for inspectors to enter the location, such as a building collapse or an oil drilling rig fire. Going forward, these may boost the capacity for safety inspections beyond what is presently possible.
Lastly, the systematic collection and analysis of reliable and comparable data have varied, making data and trend comparisons a challenging task. Thus, it is critically important for stakeholders to establish effective OSH data collection mechanisms or systems aimed at improving the collection and utilization of reliable OSH data for reporting and analysis.
Steven John Cumper founded Medshop and remains involved as the Managing Director.