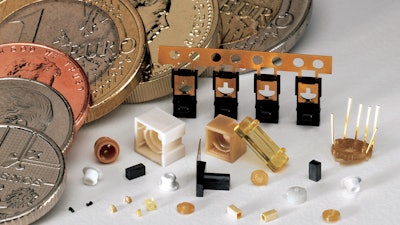
The world is getting smaller. As a result, many industries are specifying increasingly smaller components as well as larger parts with very fine features. As these emerging technologies strive to provide greater value in a smaller footprint, the design can only move forward if the components are manufacturable.
Micro molding is pushing the limits of micro-sized plastic parts. When engineers hear that their design is too small, too complex, or their tolerances are just too tight, micro molding offers a solution for achieving such tight tolerances.
In this exclusive interview, Aaron Johnson, vice president of marketing and customer strategy at Accumold, discusses the industries pushing the envelope, common misconceptions surrounding micro molding and if we've already achieved the smallest possible part.
David Mantey: What is micro molding?
Aaron Johnson: There really isn't a textbook answer, but we have come to define micro molding over the years in one of three ways:
1. Micro in size: Small parts under a centimeter or even under a millimeter would qualify as micro.
2. Larger parts with micro features: One of the largest parts we mold is about 9 cm long and has 100-micron-wide microfluidic channels molded right into the main body. While the part is large, the critical geometry is not, making this a very difficult part to build and process.
3. Micro in tolerance: Many projects we see have very tight tolerances – in some cases, only a couple of microns. This can be very challenging if you're not familiar with producing components at this level – including the metrology requirements.
We often see all three in a single project – micro parts with micro features and tight tolerances.
The bottom line is there is usually a compelling reason why you connect with a micro molder. It's usually because your current supply chain is telling you that your design is too small, too complex, or the tolerances are just too tight.
Mantey: What industries are pushing the envelope when it comes to using micro-molded components?
Johnson: A growing number of industries are interested in using micro molded components. It sounds cliche, but the world is still getting smaller. Industries like medical device, microelectronics, micro-optics, sensors, wearables and other emerging technologies are all seeking to provide more value to their customers in smaller spaces.
Cellphones these days seem to have leveled out in overall form factor, but what's going on inside continues to evolve. Higher functionality, more features and better designs are a result of micro-technologies, like micro molding, that continue to push to the limits.
Mantey: What specific medical device applications call for these types of components?
Johnson: Diagnostics, drug delivery, surgical tools, wearables and other next-generation medical devices are common examples where the smaller-the-better is often the goal. For example, a minimally invasive surgical tool that can deploy better therapies in smaller spaces is often better for patient outcomes.
However, this goal puts a lot of pressure on the supply chain for smaller and smaller components. This is one reason why micro molding is a highly sought-after service for OEMs and contract manufacturers building new medical devices.
Mantey: What are the common misconceptions when it comes to the capabilities of micro-molded parts?
Johnson: We hear all the time, 'I didn't know you could do that with plastic.' When it comes to pushing the limits with micro-sized parts and features, it often boils down to the experience of the micro molder. There isn't an easy-to-follow guide when it comes to micro plastics.
For example, understanding the relationship at the micro-level between material selection and the geometry of the design is not something you can just look up in a book. It comes from years of experience working with these materials. We always tell our customers to start with their "ideal." Start with what you think you need, and we'll have the conversation from there. Customers are often surprised at where they can push the limits, thus advancing their technology.
Mantey: What is the most interesting application you've seen use these tiny components?
Johnson: One of the most interesting applications we've molded was for a laser photonics package. We were asked to make an alignment spacer that could hold a glass bandpass filter for the laser. This part was the last little puzzle piece for aligning all the components correctly. The tough part was that the component was only 800 microns long. This was also a case where handling the part was harder than the molding.
An alignment spacer only 800 microns long. Molded with mineral filled LCP.Accumold
Mantey: Despite their small size, are there any concerns regarding the environmental impact of these parts?
Johnson: Certainly, by comparison, micro plastics have less effect on the environment, but waste is still waste. At Accumold, we are always conscientious about our impact. We are ISO 14001 certified and make a point to be as efficient as possible in all areas of our business.
Efficiency is a main benefit of our micro molding systems. Our original micro molding presses were designed almost 40 years ago to reduce the waste that normally would be associated to make such small components on larger presses. We were the leaders in building extremely efficient systems for micro plastic molding, and we've kept that as our main driver this whole time.
Mantey: What's next for the industry?
Johnson: Speed. It's always been a challenge to prototype for components that require such high precision. Prototyping micro plastic parts would often require the need to build hard steel molds to get the accuracy results needed. The cost and timing of short-run, high-precision molding can be prohibitive. This has put a lot of pressure on R&D to come up with efficient ways to prove out their designs.
New advancements in additive manufacturing (AM) have helped the industry tremendously in the last couple of years. Being able to print micro parts and tools with high precision allows designers to be more creative and also get to market faster and more efficiently. Micro AM has great potential for the future of design in micro molding.
Mantey: At some point, the parts can't get any smaller, right?
Johnson: Yes, there is a physical limitation, even if it's just the resin itself. I don't think we've seen the smallest yet. Our customers are always challenging us to go beyond.