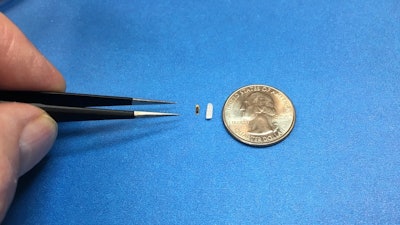
Designing and developing implantable medical devices involves navigating complex technical challenges while ensuring the highest standards of patient safety and device performance. For companies like Injectsense, creating an implantable device that can function reliably within the human body is an intricate task that requires expertise in multiple areas, including biocompatibility, miniaturization, and real-time data transmission.
Injectsense's innovative product IOP-Connect, an implantable eye pressure sensor, is designed to address intraocular pressure (IOP) management in patients with glaucoma. By providing continuous, real-time monitoring of eye pressure fluctuations—without patient intervention—this sensor plays a critical role in managing glaucoma, a leading cause of blindness worldwide.
Through the collaboration between Injectsense and Promex in developing this ultraminiaturized IOP sensor, we highlight the essential technical considerations in designing, developing, and manufacturing implantable devices.
1. Device Design: Precision Engineering for Long-Term Performance
When designing an implantable device, the primary goals are functionality, durability, and minimal invasiveness. The IOP-Connectâ„¢ sensor, which measures just 4mm in length and 1.5mm in diameter, is specifically engineered to continuously monitor the pressure inside the eye, critical for patients suffering from glaucoma.
Elevated IOP is one of the main risk factors for glaucoma, and continuous monitoring helps to detect fluctuations that can be addressed by drug therapy to prevent damage to the optic nerve. This sensor is designed to be implanted within the eye to provide consistent, real-time data without requiring invasive procedures or frequent visits to healthcare providers.
Key Technical Considerations:
- Miniaturization: Implantable devices must be small enough to minimize trauma during implantation and avoid interfering with the body's normal functions. IOP-Connect's small form factor—achieved through advanced microfabrication techniques—ensures minimal invasiveness. This is particularly critical for ocular implants where space is limited, and precision is key. The miniaturization is enabled by leveraging silicon-based pressure sensing technology, which allows for precise, accurate measurements of absolute pressure while maintaining a small footprint, essential for integration within the eye's delicate structures.
- Battery Life and Power Consumption: Implantable devices like IOP-Connect must be designed for long-lasting battery life without needing frequent replacements. By optimizing the power consumption of the sensor through energy-efficient components and low-power wireless transmission protocols, the device can function reliably for an extended period. The integration of Promex's design for the PCB inside the external reader ensures that the sensor remains efficient without compromising performance.
- Environmental Durability: Implantable sensors must be durable enough to withstand the body's constant physiological changes. It was imperative to ensure the sensor's housing was resistant to bodily fluids, temperature fluctuations, and potential chemical interactions in the eye. The materials used were carefully selected to prevent any adverse reactions, in line with ISO 10993 biocompatibility standards. The external housing of the sensor is crafted from biocompatible materials such as titanium and medical-grade polymers, which offer corrosion- and degradation-resistance within the aqueous environment of the eye.
2. Collaboration and Prototyping: Transforming Concepts Into Clinical-Grade Devices
As the design evolves, prototyping is critical in refining implantable devices to ensure they meet safety and performance standards, especially when evolving from preclinical to clinical-grade devices. Promex's expertise in developing custom manufacturing processes allowed for precise control over the device's quality during prototyping.
Key Technical Consideration:
- Testing for Safety and Efficacy: Implantable devices must undergo rigorous testing to ensure patient safety. Injectsense's preclinical device was first tested in rabbits at a major eye institute in Baltimore, where it demonstrated no adverse effects such as infection or inflammation. Following this, we produced a human-grade device that could be used in human studies. These studies were critical for establishing the safety and efficacy of the device in real-world conditions. Injectsense also utilizes accelerated aging tests to predict the long-term reliability of the sensor, assessing its functionality and stability over time in simulated human conditions.
The Injectsense IOP-Connect Sensor Platform sensors in a custom carrier.Injectsense
3. Manufacturing Considerations: From Prototype to Full-Scale Production
As the device progresses toward clinical trials and eventual commercialization, scaling up production without compromising quality is a critical challenge. Manufacturing must meet stringent regulatory requirements while ensuring that every device is free from defects.
Key Technical Consideration:
- Component Integration: Integrating multiple components, such as the sensor and the external reader system, requires careful coordination. Injectsense's reader uses both digital and analog systems, which must be compatible regarding power consumption and data transmission. We designed the PCB for the external reader and system, ensuring it could communicate wirelessly with the implanted sensor while maintaining an efficient power profile. We also considered the optimal distance between the sensor and the reader—currently an inch and a half—enabling reliable data transmission from within the eye to an external device. The sensor also incorporates MEMS (Micro-Electromechanical Systems) technology, which allows for precise, low-power, and reliable pressure measurements with a minimal footprint.
4. Data Collection and Real-Time Monitoring: Integration of Wireless Technology
Implantable devices provide a unique opportunity for continuous data collection and real-time patient monitoring, providing valuable insights to clinicians. Tracking a patient's IOP remotely ensures that potential issues are caught early, improving treatment outcomes.
Key Technical Consideration:
- Wireless Data Transmission: For an implantable device to be effective, it must be able to communicate with external systems without requiring cumbersome connections. Injectsense's sensor sends data wirelessly to an external reader, which connects to a mobile application. This data transmission must be both reliable and secure. Promex helped integrate a wireless communication protocol and ensure that the external system could transmit data to the cloud, where healthcare providers will be able to remotely access the information in real time. The device uses Bluetooth Low Energy (BLE) for power-efficient data transmission, ensuring that the patients and doctors can easily monitor IOP without interruption.
- Patient-Friendly Interface: Given that the target demographic for this device is older patients, the user interface of the mobile app was designed to be intuitive and simple. The app features a large, easy-to-press button that allows patients to check their IOP with a single push. Data is then transmitted to the cloud, ensuring that doctors can monitor patients remotely without requiring frequent in-person visits. The mobile app also features real-time alerts, which notify both patients and clinicians if the IOP exceeds critical thresholds, enabling immediate intervention.
- Cloud Infrastructure: To support the global, distributed nature of patient care, data from the device is uploaded to the cloud, where it can be accessed by healthcare providers, regardless of location. This system must adhere to data privacy regulations, including HIPAA in the U.S., ensuring that patient data remains secure. Cloud infrastructure is designed with redundancy and failover capabilities to guarantee continuous data availability.
5. AI and Machine Learning: Enhancing Manufacturing and Design Processes
The integration of AI and machine learning (ML) into medical device manufacturing is becoming increasingly essential, enabling optimization of production processes, improving device reliability, and streamlining design iterations. At a minimum, using AI and ML, there is access to global research on the condition your device addresses and the ability to find and analyze reams of existing data that already exist, for key findings related to the problem you're trying to solve.
Key Technical Consideration:
- AI for Manufacturing Optimization: One of the challenges in manufacturing implantable devices is ensuring consistency and quality across large production runs. By using AI tools, manufacturers can track performance data and identify trends in the production process, helping to detect potential quality issues before they affect the final product. Promex's implementation of AI-driven quality control processes allows Injectsense to maintain high standards while scaling up production. AI algorithms also aid in process optimization by adjusting manufacturing parameters in real time to improve yield and reduce defects.
- Machine Learning for Performance Analysis: AI can also be used to analyze device performance and make design adjustments based on real-time data. For example, ML algorithms can analyze battery life across different units to predict when batteries are likely to fail. These insights also help refine future iterations of the device design to optimize power consumption and increase reliability.
- AI-Driven Design Iterations: We plan to integrate AI more deeply into our design phases to quickly assess the impact of design changes. This involves using AI to analyze the performance of different design iterations, providing insights into how small adjustments can affect the device's overall function and longevity.
Designing and manufacturing implantable devices is an inherently complex process that requires expertise in several technical domains, including materials science, microelectronics, wireless communication, and data security. Choose members of the team for the commercialization of your implantable based on their ability to navigate these challenges successfully.
Dave Fromm is chief operating officer and vice president of engineering at Promex.Promex
Dave Fromm is chief operating officer and vice president of engineering at Promex, the market leader in microelectronic assembly for the medtech and biotechnology markets. Promex partners with OEMs at all stages, from early prototypes to R&D development and high-volume production.
Ariel Cao is co-founder, president, and CEO of Injectsense.Injectsense